There is a misconception among professional inspectors that a remote inspection over a video screen will not be as effective as a session conducted by a person that is onsite. Professional inspectors, clients, and project managers with many years of experience with onsite inspections may have adversity to switching to remote video inspections for various reasons. There are common misconceptions about the benefits of remote video inspection solutions vs. onsite inspections. This article debunks and deconstructs the common misunderstandings based upon the author’s experience with thousands of successfully completed remote video inspections.
Reason 1: Photographed or recorded inspection evidence can be reviewed more thoroughly
There is an adage in the world of photography that, “The eye is an optimist, and the lens is a pessimist.” This same sentiment holds true in the world of Remote Inspection. Often-times, the camera picks up details that the human eye glances over. Take for example my receding hairline. It’s glaring to me when I see a video or photo of it, but when I look in the mirror it doesn’t bother me. Problems with quality control can also stand out more brightly when captured in a photo or video. This is due to the fact that still images and even captured videos will give the observer more time to reflect on what is being displayed in front of them.
While it is true that the image quality of video conferencing sessions has been poor in the past, this is no longer the case when using CloudVisit. Following a great deal of user acceptance testing, and feedback, CloudVisit has managed to improve video quality greatly within the Video Conference experience. As a result, Remote Video Inspection within a CloudVisit session is now available in HD. Furthermore, the enhanced collaborative experience can even surmount an internet connection that would have once resulted in a dropped call. The improved clarity within CloudVisit’s software makes it possible to clearly see finite detail. This ensures that Inspectors can accurately identify potential deficiencies. Therefore, the opinion that reviewing work scope on screen is inferior to having boots on the ground, is simply outdated.
Reason 2: Enhanced Opportunities for Quality Audits
The beauty of a Remote Inspection is that it allows inspectors to capture and record evidence, and then easily store it for later review. So even if something was missed during the initial inspection process, a recording of the walkthrough has been captured and can be reviewed later for accuracy. This can be a double-edged sword for professional inspectors. In some cases, a remote inspection can prove that the project was completed correctly the first time, and that a deliverable later broke due to normal wear and tear. That’s certainly a plus for client management. However, in other cases, further review of video documentation can demonstrate that the inspector did a poor job initially, and a key quality control issue was overlooked. This concern for job security can be a sticking point for lackluster employees everywhere. However, management should not fall into the trap of maintaining the status quo to placate the labor pool. The absolute ease of quality auditing a remote inspection and improving operational efficiency will continue to validate the new method’s effectiveness and ultimately result in the process becoming an industry norm.
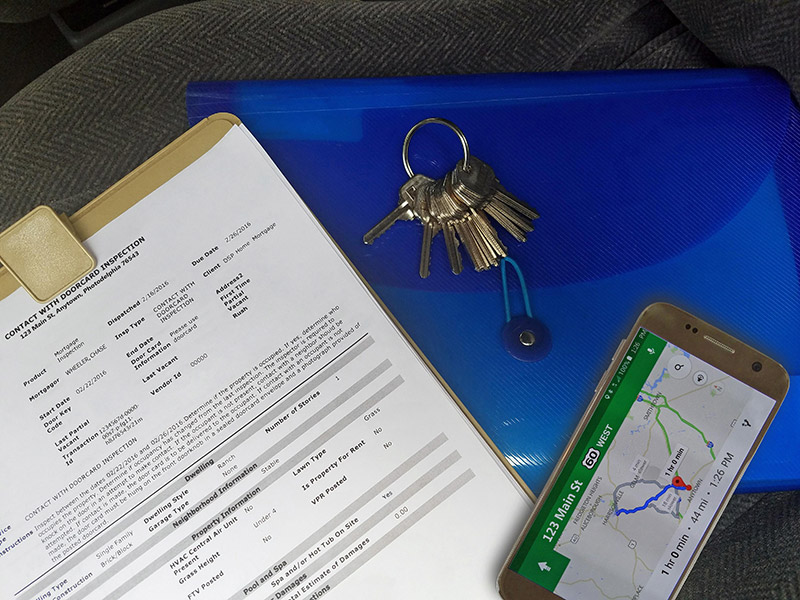
Resulting business implications from video inspections
The truth is that more and more companies are using Remote Inspection. What started as a niche market for hazardous environments within industries like Nuclear Power, has been adopted by all sorts of construction managers. For example, players like the telecom industry are now using Remote Inspection for the high profile 5G buildout.
As a result, there is now dedicated video conference inspection software available from CloudVisit. The software streamlines the process of inspection using customizable checklists, which can be based upon Inspection and Test Plans, (ITP). Furthermore, all completion evidence can be consolidated in one location or even integrated into other enterprise cloud storage solutions like Azure for easy retrieval.
Industries such as Fire Inspection and Aviation, are already in the beginning stages of adopting Remote Inspection practices.
There are barriers for the implementation of remote video inspection solutions. Existing clients, inspectors, and project managers accustomed to onsite visits and quality control may minimize the benefits of remote video inspections for various reasons. For example, the perceived threat to one’s job or simply having to change existing business processes, which have become routine, tested, and proven can both hinder an organization’s change management. This is a common challenge in implementing new processes and ways of conducting business for employees and clients. However, with proper change management utilized, including sensitivity to potential employee and client objections; phased implementation; remote video inspections can be transformational to businesses and entire industry sectors. Ultimately, inspection professionals that become obstacles within a company’s change management dynamic will find themselves left behind. According to Datausa.io, the median age of a construction inspector is 49 years old with a large number in the field in their 50s. When professional inspectors fall prey to the fallacy that their own aging eyes are superior to a lens, they are simply allowing themselves to be replaced by a younger generation of eager professionals. Don’t let yourself be fooled by the myths regarding the viability of Remote Inspection, your career depends on it.